Background
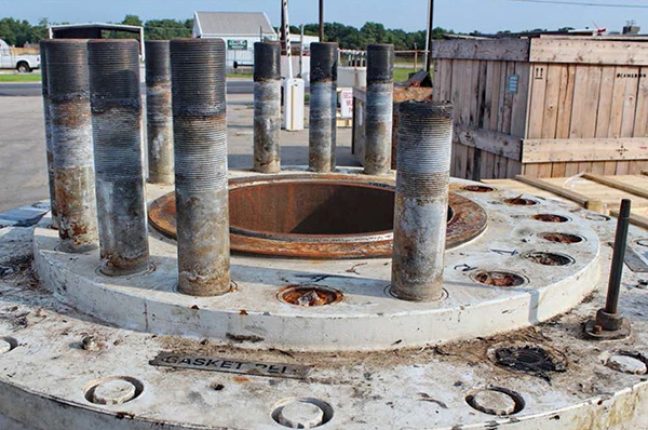
Leadership and staff of the Bureau of Safety and Environmental Enforcement have been working to address a recurring problem that raises serious safety and environmental hazard concerns - faulty connector bolts in safety critical equipment currently deployed offshore. There have been a number of failures - beginning over a decade ago around 2003 - of bolts that are used to connect blowout preventers, risers, and other subsea equipment. We have created this page so that government, industry, and other stakeholders can share the latest information related to these failures, including: root cause analyses of bolt/connector failures, safety alerts, industry standards and guidance, and other connector and bolt related information and guidance.
Under the Emerging Technology Branch, the Systems Reliability Section (SRS) observes and oversees quality-assurance and quality-control testing of offshore equipment. BSEE assembles a team of experts for the study, the Quality Control-Failure Incident Team (QC-FIT).
The BSEE formed a Quality Control Failure Incident Team to investigate the known failures and research possible causes and provide mitigation recommendations to the industry. The BSEE held a forum on August 29, 2016 with industry to discuss the failures and the results of the failure investigation, as well as ongoing research that BSEE was conducting on fastener safety. Bolt failures are a major problem in many industries, so BSEE decided to form the Interagency Bolt Action Team (IBAT) to collaborate with other industries having similar fastener failures to share the expertise, data, and experience to develop best practices on fastener safety to reduce these failures.
During drilling operations in the Gulf of Mexico (GOM), leaks were detected which identified failure, severe stress corrosion cracking fracture of bolts on the lower marine riser package (LMRP). The QC-FIT evaluated QA/QC concerns of bolts failure on the connector on a lower marine riser package (LMRP). There were QA/QC issues with second and third tier sub-contracted vendors that performed heat-treatment processes and QA/QC manufacture, design, and material properties (hardness) issues with the bolts for effective subsea operation.
After learning of the December 18, 2012 incident, BSEE worked with the operator to ensure that the company replaced any faulty bolts that were in use in equipment deployed on the Outer Continental Shelf, in a timely manner. Replacement bolts for all known H4 connectors were sent to customers worldwide. This process resulted in the replacement of more than 10,000 bolts over a relatively short time frame and short-term disruption of related deep-water activities. This report was completed and publicly released August 2014.
Key Findings and Recommendations
The failure of the GE H4 connector bolts was primarily caused by hydrogen induced stress corrosion cracking (SCC) due to hydrogen embrittlement. Bolt coatings were not processed in accordance with the latest edition of ASTM B633 coating standard. Existing industry standards do not adequately address bolting/connector performance in subsea marine applications. BSEE is working to improve industry standards by encouraging industry standard committees to develop a consistent set of standard material properties requirements for the manufacture of fasteners; Request API and ASTM further revise its relevant standards and request that industry issue guidance or a standard for the optimal voltage limits for cathodic protection systems.
- The quality management system (QMS), which met the industry standards and certification programs, qualified and audited only first-tier level suppliers and not others in the supply chain. BSEE is encouraging industry to develop an improved quality management standard that addresses multiple tier subcontractors and promoting failure reporting involving critical safety equipment.
- BSEE has initiated joint industry research initiatives that studies fastener design and fitness for service.
- BSEE may develop regulations that ensure specific design standards are met.
QC-FIT Bolt Technical Evaluations
The QC-FIT conducted several technical evaluations on subsea critical equipment fastener failures which identified global concerns related to the design, manufacture, material selection, and its performance.
- BSEE QC-FIT Update - 150114 API Winter Standards Meeting June 2016
- 2016 Update on BSEE QC-FIT Evaluation of Connectors and Bolt Failures February 2016
- QC-FIT Evaluation of Connector and Bolt Failures August 2014
QC-FIT Bolt Reports
Bolt Forum
On August 29, 2016 BSEE held a forum to present BSEE’s research and ongoing projects to the industry and to facilitate a discussion on how to move forward mitigating these bolt failures.
- BSEE Bolt Forum Presentation
- API Presentation BSEE Bolt Forum
- BSEE Bolt Forum NRC
- National Academies
- Presentation Haimei Zheng
- Video Recording Part 1 (1 hour, 42 minutes)
- Part 1 Transcript
- Video Recording Part 2 (2 hours, 3 minutes)
- Part 2 Transcript
IBAT
BSEE formed the IBAT to bring together experts from many diverse industries to collaborate and develop the best practices for the design, manufacture, material selection, and performance of fasteners.
Correspondence
BSEE has reached out to the offshore oil and gas industry and standards organizations to try to work together to mitigate the fastener failures.
- API 4Q Bolt Letter to BSEE January 31, 2019
- API 3Q Bolt Letter to BSEE_Nov.2, 2018
- API 2Q 2018 Bolt Letter to BSEE August 2, 2018
- API 1Q 2018 Bolt Letter to BSEE May 11, 2018
- API 4th Quarter Letter March 16, 2018
- API 3rd Quarter Letter November 3, 2017
- API 2nd Quarter Letter August 4, 2017
- API Final Bolts Transmittal to BSEE April 18, 2017
- API Response Letter December 9, 2016
- Bolts Response Letter to API August 25, 2016
- API Letter to BSEE Chief of Office of Offshore Regulatory Programs July 15, 2016
- BSEE SA 318 Industry Response Final Presented This was submitted to BSEE by API on March 31, 2015. BSEE staff are currently reviewing this documents
- API Response to Director Salerno March 14, 2016
- API Response to Director Salerno February 5, 2016
- Director's Letter to API January 22, 2016
- BSEE Director's Response Letter August 8, 2014
- Letter of Transmittal on Connector and Bolt Failures July 28, 2014
Related News
- API Response to Recommendations from NAS Report Oct 9, 2018
- API Comments on NAS Final Report April 6, 2018
- NAS Bolting Technology Final Report March 9, 2018
- NAS Bolt Workshop Proceedings October 17, 2017
- Bolting Reliability for Offshore Oil and Natural Gas Operations: Proceedings of a Workshop April 10-11, 2017
- Subsea Bolt Performance Workshop and Consensus Study April 6, 2017
- Bolts Team Telecon Read Out August 23, 2016
- BSEE announces Forum on Safety Equipment Failures August 1, 2016
- BSEE Director Reaches Out to Federal Agency Partners to Help Address Failures in Safety Equipment July 26, 2016
- Fact Sheet on BSEE's Subsea Bolts Performance and Critical Drill-Through Equipment Fastener Study March 2016
Related Safety Alerts
- Safety Alert: Connector and Bolt Failures February 2, 2016
- 5,000 psi Blind Shear Ram Bolting Torque Engineering Bulletin (posted with permission from GE) January 16, 2016
- Stork Stud Failure Report March 2010 This document was received by BSEE July 7, 2016
- Proposed Industry Response to BSEE Bolting Safety Alert 318 June 2016